If your Husqvarna Viking sewing machine has stopped working due to a problem and you don’t know how to fix it then keep reading.
On this page, you are going to find solutions to all the problems of a Husqvarna Viking sewing machine.
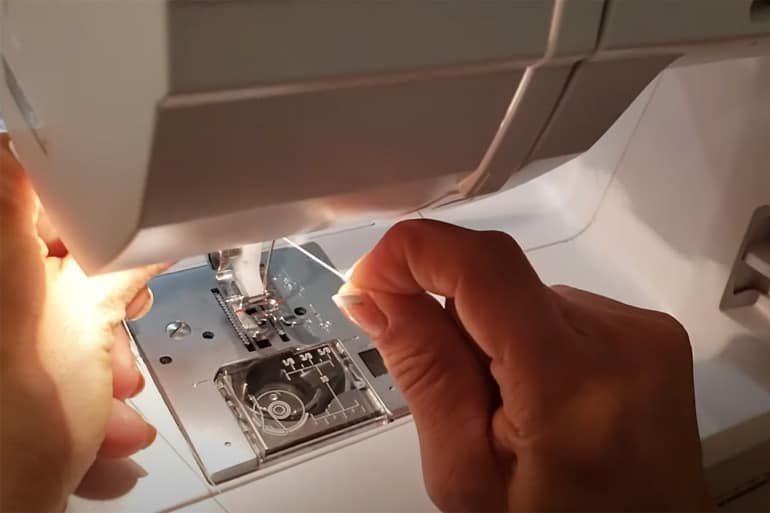
Here’s a complete list of the problems, their causes, and solutions:
Husqvarna bobbin alarm does not work
Solution:
Remove all the lint and dust from the bobbin area of your machine.
Only use the official HUSQVARNA VIKING bobbins made specifically for the sewing machine model you are currently using.
Husqvarna machine’s thread cutter is not cutting the thread
Solution:
First, remove the needle and plate and remove all the lint and dust trapped inside it.
Now go to the SET menu and enable the automatic thread cutter option.
Husqvarna sewing machine fabric does not feed
Solution:
Make sure your sewing machine is not set in the Free Motion Mode.
If it is, then change that to solve the problem.
Husqvarna machine is making wrong, narrow, or irregular stitches
Solution:
Go to the SET menu.
Deactivate the stitch width safety settings OR deactivate the twin needle.
The Husqvarna sewing machine needle keeps breaking
Solution:
Make sure you are using the right sewing needle that is not only compatible with your sewing machine but also with the fabric you are trying to sew.
Husqvarna sewing machine doesn’t sew
Solution:
Inspect your sewing machine carefully and make sure all the plugs are properly connected to your machine and the wall socket.
If any plug is loose or disconnected, then reconnect it the right way.
Husqvarna sewing machine shows a startup screen
Solution:
Activate the screen by touching it.
Go to the SET menu and turn OFF the screen saver.
Husqvarna sewing machine icons are not activated when the screen is touched
Solution:
You need to calibrate the screen to solve this problem. Go to the SET menu and you will find the Calibrate option there.
The screen or function buttons of the Husqvarna sewing machine aren’t activated upon touch
Solution:
The function buttons and sockets of Husqvarna Viking sewing machines are sensitive to static electricity.
If they are not responding upon touch, you need to turn OFF your sewing machine and then restart it. This will likely solve the problem.
But if the problem persists, you need to contact an official HUSQVARNA VIKING dealer.
Husqvarna sewing machine is skipping stitches
Cause of problem:
- The needle is not inserted correctly.
- A wrong needle is inserted.
- The needle is blunt or bent.
- A wrong presser foot is used.
- The needle is too small.
- The fabric moves up and down with the needle during embroidery or free-motion sewing.
Solution:
- Make sure you have inserted the needle correctly as per the guidelines given in the manual.
- Use the right type of needle. 130/705 needle system is ideal for the Viking sewing machine.
- Check if the needle is bent. If yes, then replace it.
- Check if your sewing machine is threaded correctly. If it is not, then rethread the machine.
- Make sure you are using the right presser foot.
- The needle size should be suitable for the thread and fabric you are working on.
- Connect the sensor Q-foot if the fabric moves up and down as described in the causes above.
Husqvarna sewing machine needle thread breaks
Cause of error:
- The needle plate hole is damaged.
- You are not using the best spool pin position.
- You are using the wrong spool cap.
- You are using a dry thread or poor thread with slubs.
- The sewing machine is not threaded correctly.
- The needle is blunt or bent.
- A wrong needle is inserted.
- The needle is not inserted correctly.
Solution:
- Try changing the needle plate.
- Try using a different spool pin position such as horizontal or vertical.
- Make sure you are using the right size of spool cap that is suitable for the thread spool.
- Always use a high-quality thread purchased from an official HUSQVARNA VIKING dealer.
- The needle size should be suitable for the thread and fabric you are working with.
- The sewing machine must be threaded correctly as per the official guidelines.
- If the needle is bent, replace it. The needle should also be of the right size and inserted correctly into the sewing machine.
Husqvarna sewing machine bobbin thread breaks
Cause of problem:
- The bobbin is not inserted correctly.
- The needle plate hole is damaged.
- The bobbin area is full of lint.
- The bobbin is not winded correctly.
Solution:
- Check the bobbin thread and make sure it is inserted correctly.
- Replace the needle plate if it is damaged.
- Clean the bobbin area thoroughly and remove all the dirt and lint trapped in there.
- The bobbin should be wound correctly.
Husqvarna sewing machine makes uneven stitches
Cause of problem:
- The thread tension is incorrect.
- The thread is slubbed or too thick.
- The bobbin thread is not wound properly.
- A wrong needle is being used.
Solution:
- Check the threading and thread tension and make sure they are right.
- Try changing the thread if it is too old or thick.
- Check the bobbin thread and make sure it is winded correctly.
- Use the right size of the needle.
Husqvarna machine is making distorted embroidery design
Cause of problem:
- The fabric is not hooped correctly.
- The inner embroidery hoop is not completely inserted into the outer embroidery hoop.
- The area around the embroidery arm is not free.
Solution:
- Make sure the fabric is tightly hooped.
- You should hoop the fabric in a way the inner hoop matches the outer hoop perfectly.
- The area around the embroidery unit should be cleared.
Husqvarna sewing machine feeds irregularly or doesn’t feed at all
Cause of problem:
- The machine is not threaded correctly.
- There is a lot of lint accumulated between the feed teeth.
- The free motion setting is turned ON.
Solution:
- Check if the sewing machine is threaded correctly. If not, then rethread the machine as per the official guidelines in the manual.
- Remove the needle plate and use a brush to clean all the lint present on the feed teeth.
- Go to the sewing mode and turn OFF the free motion settings.
Husqvarna machine is forming thread loops on the underside of embroidery designs
Cause of problem:
This is happening because the embroidery is built up too much to freely move beneath the presser foot.
Solution:
Try attaching the Q-foot sensor.
If you are using an R-foot sensor, then increase the height of the presser foot from the machine settings and SET menu until the problem is solved.
Husqvarna sewing machine is puckering the embroidery design
Cause of problem:
This happens because the fabric is not properly stabilized while sewing.
Solution:
You need to stabilize the fabric properly and the problem will be solved.
Husqvarna machine doesn’t embroider
Cause of problem:
- The embroidery unit is not attached.
- A wrong hoop is attached.
Solution:
- Check if the embroidery unit is properly connected to the socket. If not, then please connect it.
- Attach the correct hoop.
Husqvarna sewing machine sews too slow
Cause of problem:
- The machine is not cleaned.
- The machine is not lubricated.
Solution:
- Check the speed of your machine.
- Remove the stitch plate and clean all the lint and dirt present inside.
- Inspect the foot controller.
- Lubricate all the moving parts of your machine with good-quality sewing oil.
Conclusive note
If you have tried the solutions given in this article but your sewing machine is still not working, then we recommend you contact the nearest HUSQVARNA VIKING sewing machine dealer.
They will check your sewing machine completely and fix the underlying technical problems.